Material Library
Edit Cabling
Properties
Edit Material Properties
The dialog box is also available via Cable
Navigation Tree: Library
Materials.
A right mouse click on Materials
opens a drop-down menu where the user is able to call the Edit
dialog box. It shows a list of all available materials. The icons on the
top of the dialog box enable actions which are explained below. The meaning
of each icon is also explained by tool-tips. To see a tool-tip just move
the mouse-pointer over the corresponding icon:
Create a new material
Duplicate a selected material
Import materials from an external Material Library
File
Export materials into an external Material Library
File
Remove all materials which are not used within the
current project
Delete the selected materials.
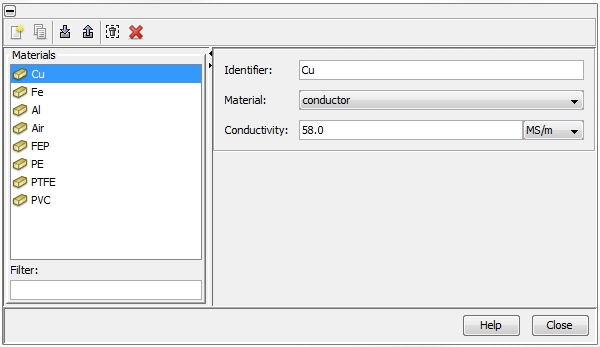
There are two different types of materials: conductor
and dielectric. Each material
requires a unique name that has to be assigned in the field Identifier.
The type of the material can be set in the field Material.
Materials of type conductor are
characterized by their conductivity which has to be set inside the field
Conductivity. The Skin effect
of a conductive material is modeled by using the
conductivity and the 2D cross-section shape of the corresponding conductor.
In case of material type dielectric,
there are two further parameters. The field Permittivity
enables the definition of the
relative permittivity and the field
Loss angle tan() enables the definition of the dielectric loss
angle. If the Loss
angle differs from zero a specific Frequency
has to be specified where the given Permittivity
is valid. The loss angle will be assumed as constant over the whole frequency
range (see Maximum
valid frequency)
Ohmic
loss modeling
The program approximates the increase in ohmic resistance and the decrease
in internal inductance over the specified frequency range, from DC up
to a maximum frequency, which is specified via the parameter Model
valid up to frequency (see Maximum
valid frequency). The way that the impedance changes over frequency
depends on the general shape of the conductor. On a PCB the typical shape
type is a flat rectangle. In general, the program distinguishes between
thin rectangle (strips) and circular wire shapes. For both shape types
CST PCB STUDIO provides a solution for the two different kinds of model
interpretation during the circuit simulation (see Circuit
Simulation Aspects).
In case of a Dispersive model
interpretation, an analytic expression
is used to describe the Skin effect
over the frequency range:

In case of a Standard model
interpretation, a multi-order R/L ladder
circuit model is used to approximate the characteristic behavior
given by the analytic expression:
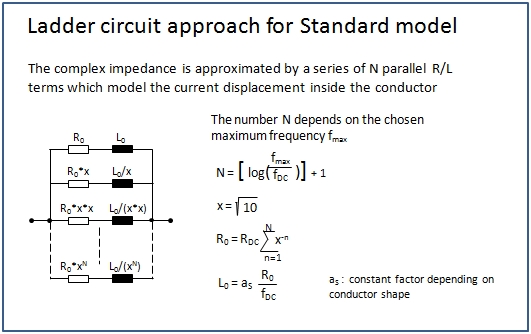
Reference:
"Experimental Researches on Skin Effect in
Conductors", A.E. Kennelly; P.H. Pierce, Panama-Pacific Convention
of the American Institute of Electrical Engineers, San Francisco, September
16.th 1915
"Digital Signal Integrity", B. Young,
Prentice Hall, 200, chapters: 7.4 and 10.3
Dielectric
loss modeling
The program approximates a constant loss angle over the specified frequency
range, from DC up to a maximum frequency (see Maximum
valid frequency). The crucial point in dielectric loss modeling is
to keep the model causal. CST PCB STUDIO provides a solution for the two
different kinds of model interpretations during the circuit simulation
(see Circuit
Simulation Aspects).
In case of a Dispersive model
interpretation, an analytic expression
is used to describe the relationship between the increase of conductance
and the decrease of capacitance over the frequency range. At the frequency,
specified in the material definition dialog box, the capacitance corresponds
to the permittivity, also specified in the material definition dialog
box.
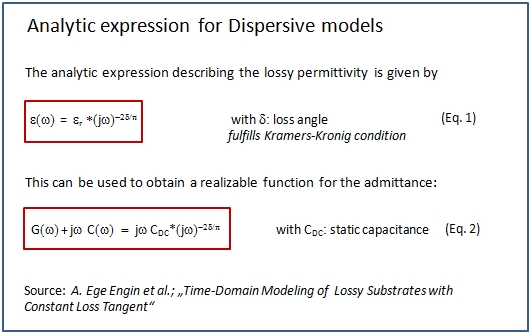
In case of a Standard model
interpretation, a multi-order Debye
model is used to approximate the characteristic behavior of the analytic
expression:

Reference:
"Time-Domain Modeling of Lossy Substrates with
Constant Loss Tangent", A.E. Engin; W. Mathis.; W. John; G. Sommer;
H. Reichl, Signal Propagation on Interconnects, Proceedings. 8th IEEE
Workshop; 9-12 May 2004, pp 151-154